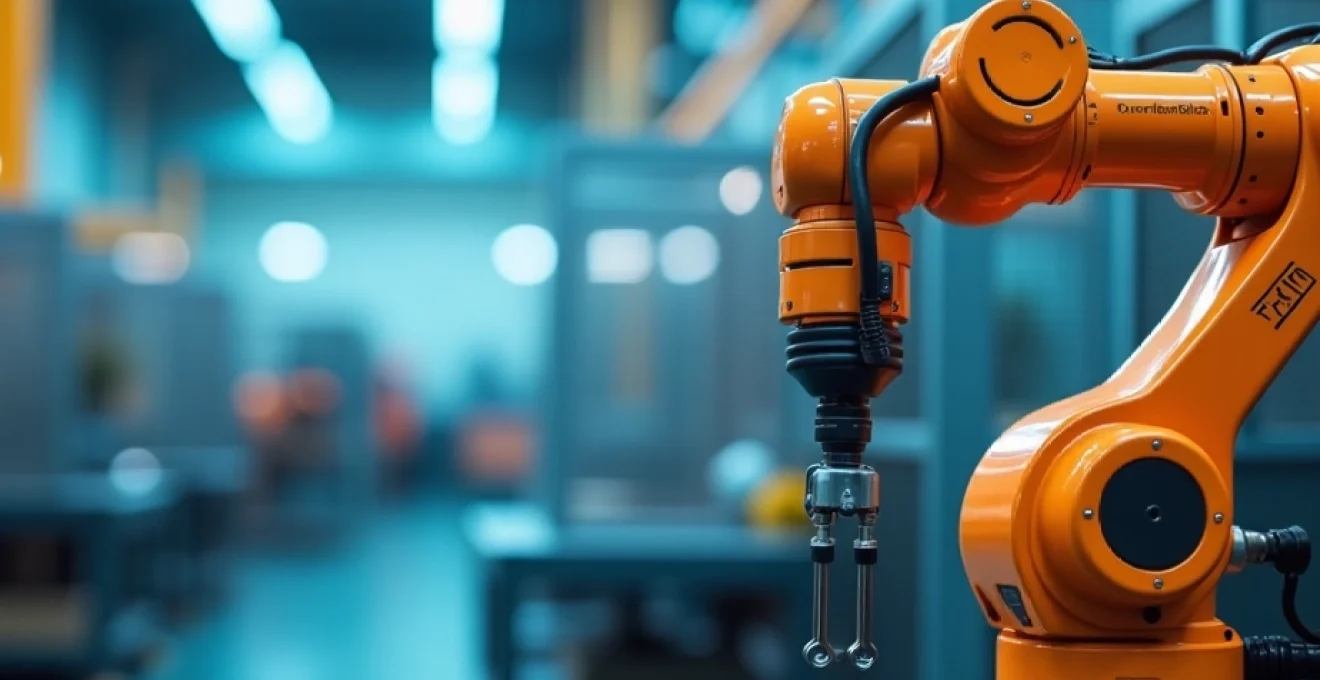
The manufacturing landscape is undergoing a profound transformation, with collaborative robotics emerging as a game-changing technology. As industries seek to enhance productivity, improve worker safety, and adapt to rapidly changing market demands, cobots are proving to be an invaluable asset. These sophisticated machines are designed to work alongside human employees, augmenting their capabilities and revolutionizing the way we approach production processes. The rise of collaborative robotics marks a significant shift from traditional automation, offering unprecedented flexibility and efficiency in manufacturing environments.
Evolution of human-robot collaboration in manufacturing
The journey of robotics in manufacturing has been a long and fascinating one. From the early days of isolated, caged industrial robots to today's sophisticated collaborative systems, the industry has witnessed a remarkable evolution. Traditional robots, while powerful and efficient, were often confined to specific tasks and separated from human workers due to safety concerns. The advent of collaborative robotics has changed this paradigm, allowing for a more integrated and synergistic approach to manufacturing.
Collaborative robots, or cobots, represent a new era in human-machine interaction. Unlike their predecessors, cobots are designed with safety features that allow them to work in close proximity to humans without the need for protective barriers. This shift has opened up new possibilities for flexible manufacturing processes, where humans and robots can complement each other's strengths. The result is a more adaptive and responsive production environment, capable of handling diverse tasks and rapid changeovers.
As manufacturing becomes increasingly complex, with demands for customization and shorter product lifecycles, the role of cobots has become more critical. These machines can be quickly reprogrammed and redeployed, making them ideal for small-batch production and frequently changing assembly lines. This flexibility is particularly valuable for small and medium-sized enterprises (SMEs) that require agile manufacturing solutions to remain competitive in a global market.
Key technologies driving collaborative robotics
The rapid advancement of collaborative robotics is underpinned by several key technologies that enable safe and efficient human-robot collaboration. These innovations have transformed cobots from simple assistants to sophisticated partners in the manufacturing process, capable of adapting to various tasks and environments.
Advanced sensors and machine vision systems
One of the cornerstones of collaborative robotics is the integration of advanced sensors and machine vision systems. These technologies allow cobots to perceive their environment with unprecedented accuracy, enabling them to navigate complex workspaces and interact safely with human co-workers. High-resolution cameras and 3D sensors provide cobots with real-time visual data, allowing them to identify objects, detect obstacles, and make split-second decisions to avoid collisions.
Machine vision systems have become increasingly sophisticated, incorporating deep learning algorithms that enable cobots to recognize patterns and adapt to changing conditions. This capability is particularly valuable in quality control applications, where cobots can perform visual inspections with a level of consistency and precision that surpasses human capabilities. As these systems continue to evolve, we can expect cobots to become even more adept at complex tasks that require visual acuity and decision-making.
Force-torque sensing for safe human interaction
Force-torque sensing technology is another crucial element that enables safe and effective collaboration between humans and cobots. These sensors allow robots to detect and respond to physical contact, adjusting their movements to prevent injury to human workers. By continuously monitoring the forces applied during operation, cobots can work alongside humans without the need for protective barriers, significantly enhancing workplace flexibility and efficiency.
The implementation of force-torque sensing has opened up new possibilities for delicate assembly tasks and precise material handling. Cobots equipped with this technology can perform tasks that require a gentle touch, such as inserting fragile components or working with soft materials. This level of sensitivity was previously the domain of human workers alone, but now cobots can complement human skills in these areas, leading to improved product quality and reduced fatigue for workers.
Artificial intelligence and machine learning integration
The integration of artificial intelligence (AI) and machine learning (ML) into collaborative robotics represents a significant leap forward in cobot capabilities. These technologies enable cobots to learn from experience, optimize their performance over time, and even anticipate the needs of their human counterparts. AI-powered cobots can analyze vast amounts of data to identify patterns and make informed decisions, leading to improved efficiency and reduced errors in manufacturing processes.
Machine learning algorithms allow cobots to adapt to new tasks quickly, reducing the time and cost associated with reprogramming. This adaptability is particularly valuable in dynamic manufacturing environments where product specifications and production volumes may change frequently. As AI and ML technologies continue to advance, we can expect cobots to become even more autonomous and capable of handling complex, multi-step processes with minimal human intervention.
Intuitive programming interfaces for non-experts
One of the most significant barriers to the adoption of robotics in manufacturing has been the complexity of programming and operation. Collaborative robotics is addressing this challenge through the development of intuitive programming interfaces that allow non-experts to easily configure and deploy cobots. These user-friendly interfaces often utilize graphical programming languages or teach-by-demonstration techniques, enabling workers with minimal technical expertise to program cobots for specific tasks.
The simplification of cobot programming has democratized automation, making it accessible to a broader range of manufacturers, including SMEs that may not have dedicated robotics experts on staff. This ease of use not only reduces implementation costs but also empowers workers to take a more active role in optimizing production processes. As programming interfaces become even more intuitive, we can expect to see a wider adoption of collaborative robotics across various industries and applications.
Safety standards and protocols for cobot implementation
As collaborative robots become more prevalent in manufacturing environments, ensuring the safety of human workers remains paramount. The development and implementation of robust safety standards and protocols are crucial for the successful integration of cobots into the workplace. These guidelines not only protect employees but also provide a framework for manufacturers to confidently deploy collaborative robotics solutions.
ISO/TS 15066 compliance for collaborative robots
The International Organization for Standardization (ISO) has developed specific technical specifications for collaborative robots, known as ISO/TS 15066. This standard provides detailed guidance on the safety requirements for collaborative robotic systems, including risk assessment procedures and performance requirements. Compliance with ISO/TS 15066 ensures that cobots are designed and implemented in a way that minimizes the risk of injury to human workers.
Key aspects of ISO/TS 15066 include specifications for maximum allowable force and pressure limits during human-robot contact, as well as guidelines for the implementation of safety-rated monitored stop functions. Manufacturers and integrators must carefully consider these requirements when designing and deploying collaborative robotic systems to ensure they meet or exceed the safety standards set forth by the ISO.
Risk assessment methodologies for human-robot workspaces
Implementing collaborative robots requires a thorough risk assessment of the entire workspace. This process involves identifying potential hazards, evaluating the likelihood and severity of potential injuries, and implementing appropriate safety measures. Risk assessment methodologies for human-robot workspaces typically include:
- Task analysis to understand the specific operations and movements of both humans and cobots
- Hazard identification to pinpoint potential sources of injury or accidents
- Risk estimation to quantify the level of risk associated with each identified hazard
- Risk evaluation to determine if additional safety measures are required
- Implementation of risk reduction strategies, such as adjusting cobot speed or implementing additional sensors
By conducting comprehensive risk assessments, manufacturers can create safer work environments that maximize the benefits of collaborative robotics while minimizing potential dangers to human workers.
Emergency stop and power limiting features
Emergency stop systems and power limiting features are critical components of cobot safety protocols. Emergency stop buttons must be easily accessible to workers and, when activated, should immediately halt all cobot movements. These systems are designed to provide a rapid response to potential safety hazards, allowing human operators to quickly intervene if necessary.
Power limiting features, on the other hand, are built into the cobot's design to ensure that even in the event of a collision, the force exerted by the robot is not sufficient to cause injury. This is typically achieved through a combination of lightweight materials, compliant joints, and sophisticated control systems that can detect and respond to unexpected contact. By implementing these safety features, manufacturers can create a collaborative workspace where humans and robots can work together efficiently and securely.
Ergonomic and productivity enhancements with cobots
One of the most significant benefits of collaborative robotics in manufacturing is the potential for ergonomic improvements and productivity enhancements. Cobots can take on tasks that are physically demanding, repetitive, or require awkward postures, reducing the risk of musculoskeletal disorders among human workers. This not only improves worker health and satisfaction but also leads to increased overall productivity and quality of output.
By delegating repetitive or strenuous tasks to cobots, human workers can focus on higher-value activities that require creativity, problem-solving, and decision-making skills. This division of labor plays to the strengths of both humans and machines, creating a more efficient and effective manufacturing process. Additionally, cobots can maintain consistent performance over long periods, reducing errors and improving product quality.
The implementation of cobots has shown remarkable results in various industries. For example, in automotive manufacturing, cobots have been used to assist with tasks such as applying sealants or installing small components, reducing worker strain and improving precision. In electronics assembly, cobots equipped with vision systems can perform intricate soldering tasks with a level of consistency that is difficult for humans to match over extended periods.
Industry-specific applications of collaborative robots
Collaborative robots have found applications across a wide range of manufacturing sectors, each with its unique requirements and challenges. Let's explore some industry-specific examples of successful cobot implementations:
Automotive assembly: BMW's use of KUKA LBR iiwa
BMW has been at the forefront of integrating collaborative robots into their production lines. The company has implemented KUKA's LBR iiwa cobots in various assembly tasks, including the installation of door seals. This application demonstrates how cobots can work alongside human operators in tight spaces, performing tasks that require both precision and force. The LBR iiwa's sensitive force-torque sensors allow it to apply the correct pressure when fitting the seals, ensuring a perfect fit every time while reducing the physical strain on human workers.
Electronics manufacturing: Foxconn's implementation of ABB YuMi
Foxconn, a major electronics manufacturer, has incorporated ABB's YuMi cobots into their production processes. YuMi is a dual-arm cobot specifically designed for small parts assembly and has proven particularly effective in the electronics industry. At Foxconn, YuMi cobots assist in tasks such as placing components on circuit boards and performing quality control checks. The precision and consistency of these cobots have led to improved product quality and reduced error rates in electronics assembly.
Aerospace: Airbus's deployment of Universal Robots UR10
Airbus has integrated Universal Robots' UR10 cobots into their aircraft manufacturing processes. These cobots are used for tasks such as drilling holes in aircraft fuselages and applying sealant. The flexibility of the UR10 allows it to be easily reprogrammed for different aircraft models, making it an ideal solution for the aerospace industry's need for adaptable automation. By using cobots for these repetitive and precision-demanding tasks, Airbus has improved both the quality and consistency of their manufacturing processes.
Pharmaceutical production: Novartis's adoption of Rethink Robotics' Sawyer
In the pharmaceutical industry, Novartis has implemented Rethink Robotics' Sawyer cobots in their production facilities. These cobots are used for tasks such as handling sensitive materials and performing precise measurements. The Sawyer cobot's ability to work in sterile environments and its easy programming interface make it well-suited for the stringent requirements of pharmaceutical manufacturing. By automating these critical tasks, Novartis has improved the consistency and reliability of their production processes while maintaining the highest standards of quality and safety.
Economic impact and ROI of collaborative robotics in manufacturing
The adoption of collaborative robotics in manufacturing has demonstrated significant economic benefits and return on investment (ROI) for companies across various industries. While the initial investment in cobot technology can be substantial, the long-term financial advantages often outweigh the costs. Here are some key economic considerations:
Increased productivity is one of the primary drivers of ROI for collaborative robotics. Cobots can work continuously without breaks, leading to higher output and improved efficiency. Many manufacturers report productivity gains of 50% or more after implementing cobots in their production lines. This increase in output can lead to faster time-to-market and improved competitiveness.
Quality improvements also contribute significantly to the economic benefits of cobots. By performing tasks with consistent precision, cobots can reduce error rates and minimize waste. This not only saves on material costs but also enhances customer satisfaction and brand reputation. Some companies have reported defect rate reductions of up to 90% in cobot-assisted processes.
Labor cost savings are another important factor in the ROI calculation for collaborative robotics. While cobots are not intended to replace human workers entirely, they can take on repetitive or physically demanding tasks, allowing companies to allocate human resources more efficiently. This can lead to reduced overtime costs and lower turnover rates among employees who are freed from monotonous tasks.
The flexibility of cobots also contributes to their economic value. Unlike traditional automation systems, cobots can be easily reprogrammed and redeployed for different tasks or production lines. This adaptability is particularly valuable for manufacturers dealing with frequent product changes or seasonal variations in demand. The ability to quickly reconfigure cobots can lead to significant cost savings compared to investing in multiple specialized machines.
While the specific ROI of collaborative robotics can vary depending on the application and industry, many manufacturers report payback periods of less than two years for their cobot investments. As the technology continues to advance and become more affordable, we can expect to see even shorter payback periods and greater economic benefits for adopters of collaborative robotics in manufacturing.