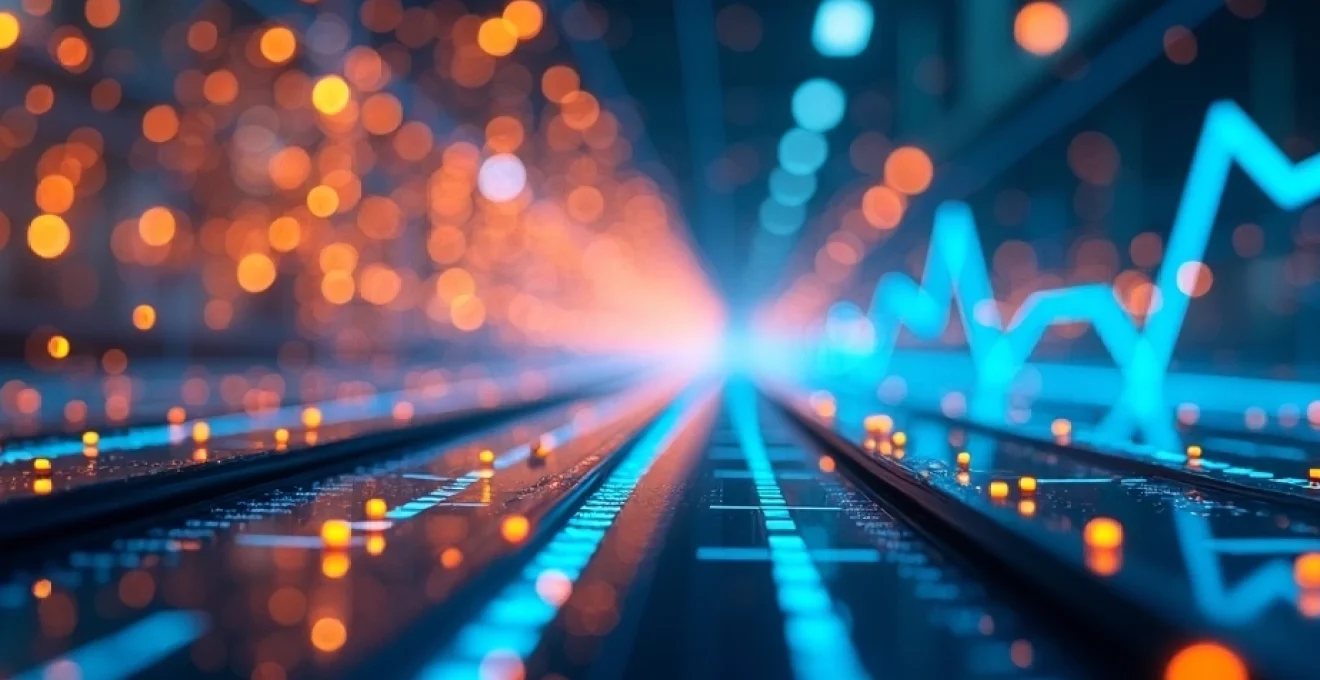
Predictive manufacturing is revolutionizing the industrial landscape, offering unprecedented opportunities to minimize downtime and slash operational costs. By harnessing the power of advanced analytics, machine learning, and real-time data processing, manufacturers can anticipate equipment failures, optimize production schedules, and streamline supply chains like never before. This proactive approach not only enhances efficiency but also significantly boosts the bottom line, making it a game-changer for businesses striving to stay competitive in today's fast-paced market.
Machine learning algorithms in predictive manufacturing
At the heart of predictive manufacturing lies a sophisticated array of machine learning algorithms. These powerful tools analyze vast amounts of data to identify patterns, predict outcomes, and make intelligent decisions. By leveraging techniques such as neural networks, support vector machines, and decision trees, manufacturers can gain invaluable insights into their operations.
One of the most significant applications of machine learning in this context is predictive maintenance. By analyzing historical data and real-time sensor readings, algorithms can predict when a piece of equipment is likely to fail, allowing maintenance teams to intervene before costly breakdowns occur. This proactive approach can reduce unplanned downtime by up to 50% and extend machine life by 20-40%.
Moreover, machine learning algorithms can optimize production schedules by considering multiple variables simultaneously. For instance, they can factor in raw material availability, energy costs, and demand forecasts to create the most efficient production plan. This level of optimization can lead to a 20-30% reduction in production costs and a significant increase in overall equipment effectiveness (OEE).
Real-time data analytics for equipment monitoring
Real-time data analytics forms the backbone of predictive manufacturing, providing a continuous stream of information that enables rapid decision-making and immediate response to potential issues. This approach transforms traditional manufacturing processes into agile, responsive systems capable of adapting to changing conditions on the fly.
Implementing IoT sensors for continuous data collection
The Internet of Things (IoT) has ushered in a new era of data collection in manufacturing. By deploying a network of smart sensors across the production floor, manufacturers can gather a wealth of information on equipment performance, environmental conditions, and production metrics. These sensors can monitor parameters such as temperature, vibration, pressure, and energy consumption, providing a comprehensive view of the manufacturing process.
For example, a typical automotive production line might have over 1,000 IoT sensors, each collecting data every millisecond. This granular level of monitoring allows for the detection of even the slightest anomalies that could indicate impending equipment failure. By addressing these issues proactively, manufacturers can reduce maintenance costs by up to 40% and increase machine availability by 20%.
Edge computing solutions for rapid processing
While IoT sensors provide a wealth of data, the sheer volume can overwhelm traditional centralized computing systems. This is where edge computing comes into play. By processing data closer to its source, edge computing solutions can dramatically reduce latency and enable real-time decision-making.
In a predictive manufacturing environment, edge devices can perform initial data analysis and filtering, sending only the most relevant information to central systems. This approach not only reduces network bandwidth requirements but also allows for faster response times to critical events. For instance, an edge device could detect a dangerous temperature spike in a piece of equipment and trigger an immediate shutdown, preventing potential damage or safety hazards.
Anomaly detection using Statistical Process Control (SPC)
Statistical Process Control (SPC) is a powerful tool for detecting anomalies in manufacturing processes. By establishing control limits based on historical data, SPC can quickly identify when a process is deviating from its normal operating parameters. In the context of predictive manufacturing, SPC is often combined with machine learning algorithms to create more sophisticated anomaly detection systems.
These advanced systems can learn from past data to recognize subtle patterns that might indicate future problems. For example, they might detect a gradual increase in motor vibration that, while still within normal limits, could signal an impending bearing failure. By flagging these issues early, manufacturers can schedule maintenance during planned downtime, avoiding costly unplanned stoppages.
Predictive maintenance scheduling with Random Forest models
Random Forest models have emerged as a particularly effective tool for predictive maintenance scheduling. These ensemble learning methods combine multiple decision trees to create a robust prediction model that can handle complex, non-linear relationships in manufacturing data.
A typical Random Forest model for predictive maintenance might consider variables such as equipment age, operating hours, sensor readings, and historical failure data. By analyzing these factors, the model can predict the likelihood of equipment failure within a given time frame, allowing maintenance teams to schedule interventions at the most opportune moments.
The effectiveness of this approach is striking. Companies implementing Random Forest-based predictive maintenance have reported reductions in unplanned downtime of up to 70% and increases in equipment lifespan of 20-40%. These improvements translate directly into cost savings and enhanced productivity.
Digital twin technology for process optimization
Digital twin technology represents a quantum leap in manufacturing process optimization. By creating a virtual replica of physical assets and processes, manufacturers can simulate, analyze, and optimize their operations in a risk-free digital environment. This powerful tool enables companies to test different scenarios, identify bottlenecks, and make data-driven decisions to improve efficiency and reduce costs.
Creating high-fidelity virtual replicas of manufacturing systems
The first step in leveraging digital twin technology is creating accurate, high-fidelity virtual replicas of manufacturing systems. These digital twins incorporate real-time data from IoT sensors, historical performance data, and detailed 3D models of equipment and facilities. The result is a living, breathing digital representation of the entire manufacturing process.
Creating these virtual replicas requires a significant investment in data collection, modeling, and integration technologies. However, the payoff can be substantial. Manufacturers using digital twins have reported improvements in overall equipment effectiveness (OEE) of up to 25%, along with reductions in maintenance costs of 10-40%.
Simulating production scenarios with Monte Carlo methods
Once a digital twin is in place, manufacturers can use advanced simulation techniques like Monte Carlo methods to explore different production scenarios. These statistical techniques allow for the simulation of complex systems with multiple variables and uncertain outcomes.
For example, a manufacturer might use Monte Carlo simulation to analyze the impact of different maintenance schedules on production output and equipment lifespan. By running thousands of simulations with varying parameters, they can identify the optimal maintenance strategy that maximizes uptime while minimizing costs.
The power of this approach lies in its ability to consider a vast number of potential scenarios. A typical Monte Carlo simulation might run 10,000 or more iterations, providing a comprehensive view of possible outcomes and their probabilities. This level of analysis can lead to more informed decision-making and improved risk management.
Optimizing workflows through What-If analysis
Digital twins also enable manufacturers to perform detailed what-if analyses to optimize their workflows. By adjusting various parameters in the virtual environment, they can see how changes would impact the real-world production process without the risk and cost of physical experimentation.
For instance, a manufacturer might use their digital twin to explore the impact of adding a new production line, changing shift patterns, or implementing a new quality control process. They can assess how these changes would affect throughput, quality, energy consumption, and other key performance indicators (KPIs).
The insights gained from these analyses can be transformative. Companies using digital twins for workflow optimization have reported productivity improvements of 10-30% and reductions in time-to-market for new products of up to 50%.
Artificial intelligence in quality control and defect prediction
Artificial Intelligence (AI) is revolutionizing quality control in manufacturing, offering unprecedented accuracy and efficiency in defect detection and prediction. By leveraging computer vision, deep learning, and predictive analytics, AI systems can identify defects that might be invisible to the human eye and predict quality issues before they occur.
One of the most powerful applications of AI in quality control is in visual inspection. Advanced convolutional neural networks (CNNs) can analyze images or video streams in real-time, detecting even the most subtle defects. These systems can be trained on vast datasets of defect images, allowing them to recognize an ever-expanding range of quality issues.
For example, an AI-powered visual inspection system in an electronics manufacturing plant might be able to detect microscopic solder joint defects at a rate of thousands per minute, with an accuracy rate exceeding 99%. This level of performance far surpasses what is possible with human inspectors, leading to dramatic improvements in product quality and reductions in defect-related costs.
Beyond visual inspection, AI systems can also predict potential quality issues by analyzing data from throughout the production process. By considering factors such as raw material characteristics, equipment performance, and environmental conditions, these systems can flag batches that are at high risk of quality problems before they even reach the inspection stage.
The impact of AI on quality control can be substantial. Manufacturers implementing AI-driven quality control systems have reported reductions in defect rates of up to 90% and increases in first-pass yield of 5-20%. These improvements not only reduce costs associated with waste and rework but also enhance customer satisfaction and brand reputation.
Supply chain optimization using predictive analytics
Predictive analytics is transforming supply chain management, enabling manufacturers to anticipate demand fluctuations, optimize inventory levels, and mitigate potential disruptions. By analyzing historical data, market trends, and external factors, predictive analytics can provide valuable insights that lead to more efficient and resilient supply chains.
Demand forecasting with ARIMA and Prophet models
Accurate demand forecasting is crucial for effective supply chain management. Advanced time series models like ARIMA (Autoregressive Integrated Moving Average) and Facebook's Prophet are increasingly being used to predict future demand with high accuracy.
These models can incorporate multiple variables, including historical sales data, seasonal trends, promotional activities, and even external factors like economic indicators or weather patterns. By considering this wide range of inputs, they can generate more accurate and nuanced forecasts than traditional methods.
For instance, a consumer goods manufacturer might use an ARIMA model to forecast demand for its products across different regions. The model could consider factors such as past sales, upcoming holidays, planned marketing campaigns, and local economic conditions. This granular level of forecasting allows for more precise production planning and inventory management, reducing both stockouts and excess inventory.
Inventory management through reinforcement learning
Reinforcement learning, a branch of machine learning, is proving to be a powerful tool for optimizing inventory management. These systems can learn optimal inventory policies by simulating different scenarios and receiving feedback on their decisions.
A reinforcement learning system for inventory management might consider factors such as demand variability, lead times, storage costs, and stockout penalties. Over time, it learns to make decisions that balance the cost of holding inventory against the risk of stockouts, continuously adapting to changing conditions.
The results can be impressive. Companies implementing reinforcement learning for inventory management have reported reductions in inventory holding costs of 15-30% while maintaining or improving service levels.
Supplier performance prediction using decision trees
Predictive analytics can also be applied to supplier management, helping manufacturers anticipate and mitigate potential supply chain disruptions. Decision tree models are particularly useful in this context, as they can handle complex, multi-faceted decisions and provide easily interpretable results.
A decision tree model for supplier performance prediction might consider factors such as historical delivery times, quality metrics, financial stability indicators, and geopolitical risk factors. By analyzing these variables, the model can predict which suppliers are at risk of performance issues and suggest proactive measures to address potential problems.
This approach allows manufacturers to move from reactive to proactive supplier management, potentially avoiding costly disruptions. Companies using predictive analytics for supplier management have reported reductions in supply chain disruptions of up to 35% and improvements in on-time delivery rates of 10-20%.
Logistics optimization with genetic algorithms
Genetic algorithms, inspired by the process of natural selection, are proving to be highly effective in solving complex logistics optimization problems. These algorithms can efficiently explore vast solution spaces to find optimal or near-optimal solutions for routing, scheduling, and resource allocation challenges.
For example, a manufacturer with a complex distribution network might use a genetic algorithm to optimize its logistics operations. The algorithm could consider factors such as shipment sizes, vehicle capacities, delivery time windows, and fuel costs to determine the most efficient routing and scheduling plan.
The potential for cost savings is significant. Companies implementing genetic algorithms for logistics optimization have reported reductions in transportation costs of 10-30% and improvements in on-time delivery performance of up to 25%.
ROI analysis of predictive manufacturing implementation
While the benefits of predictive manufacturing are clear, implementing these advanced technologies requires significant investment. Conducting a thorough Return on Investment (ROI) analysis is crucial for justifying the upfront costs and ensuring long-term value creation.
The ROI calculation for predictive manufacturing should consider both tangible and intangible benefits. Tangible benefits include reductions in maintenance costs, decreased downtime, improved product quality, and increased production efficiency. Intangible benefits might include enhanced customer satisfaction, improved brand reputation, and increased employee satisfaction due to more predictable work schedules.
A comprehensive ROI analysis should also factor in the costs associated with implementing predictive manufacturing technologies. These might include hardware costs (such as IoT sensors and edge computing devices), software licenses, integration expenses, and training costs for staff.
Despite the significant upfront investment, the ROI for predictive manufacturing can be substantial. According to a study by McKinsey, predictive maintenance alone can reduce machine downtime by 30-50% and increase machine life by 20-40%. When combined with other predictive manufacturing technologies, the potential for value creation is even greater.
Consider this example: A large automotive manufacturer implemented a comprehensive predictive manufacturing system across its plants. The initial investment was $20 million, including hardware, software, and training costs. In the first year after implementation, the company saw the following results:
- 20% reduction in unplanned downtime
- 15% improvement in overall equipment effectiveness (OEE)
- 10% reduction in maintenance costs
- 5% increase in production output
- 2% improvement in product quality (reduction in defect rate)
These improvements translated to an annual cost saving of $45 million and additional revenue of $30 million. With an annual benefit of $75 million against an initial investment of $20 million, the payback period was less than four months, and the first-year ROI was 275%.
While results will vary depending on the specific industry and implementation, this example illustrates the potential for substantial returns from predictive manufacturing investments. As technologies continue to advance and become more cost-effective, the business case for predictive manufacturing is likely to become even more compelling.
Predictive manufacturing represents a paradigm shift in how industries approach production, maintenance, and supply chain management. By leveraging advanced technologies such as machine learning, IoT, and digital twins, manufacturers can dramatically reduce downtime, optimize costs, and improve overall operational efficiency. While the implementation of these technologies requires significant investment and organizational change, the potential returns in terms of cost savings, productivity improvements, and competitive advantage make predictive manufacturing an increasingly essential strategy for forward-thinking companies in today's rapidly evolving industrial landscape.